Digital Transformation Keeps Manufacturers at the Forefront of Technology
Some manufacturers have been reluctant to embrace Industry 4.0 and the Internet of Things (IoT)—but Covid-19 changed all that. The pandemic was a test of a company’s agility, awareness, problem-solving, and resiliency. In general, manufacturers that turned to technology—sensor systems, automation, robotics, machine-to-machine learning, artificial intelligence (AI), predictive maintenance, and real-time data analytics through cloud-based platforms that connect facilities around the world—did better than those that did not.
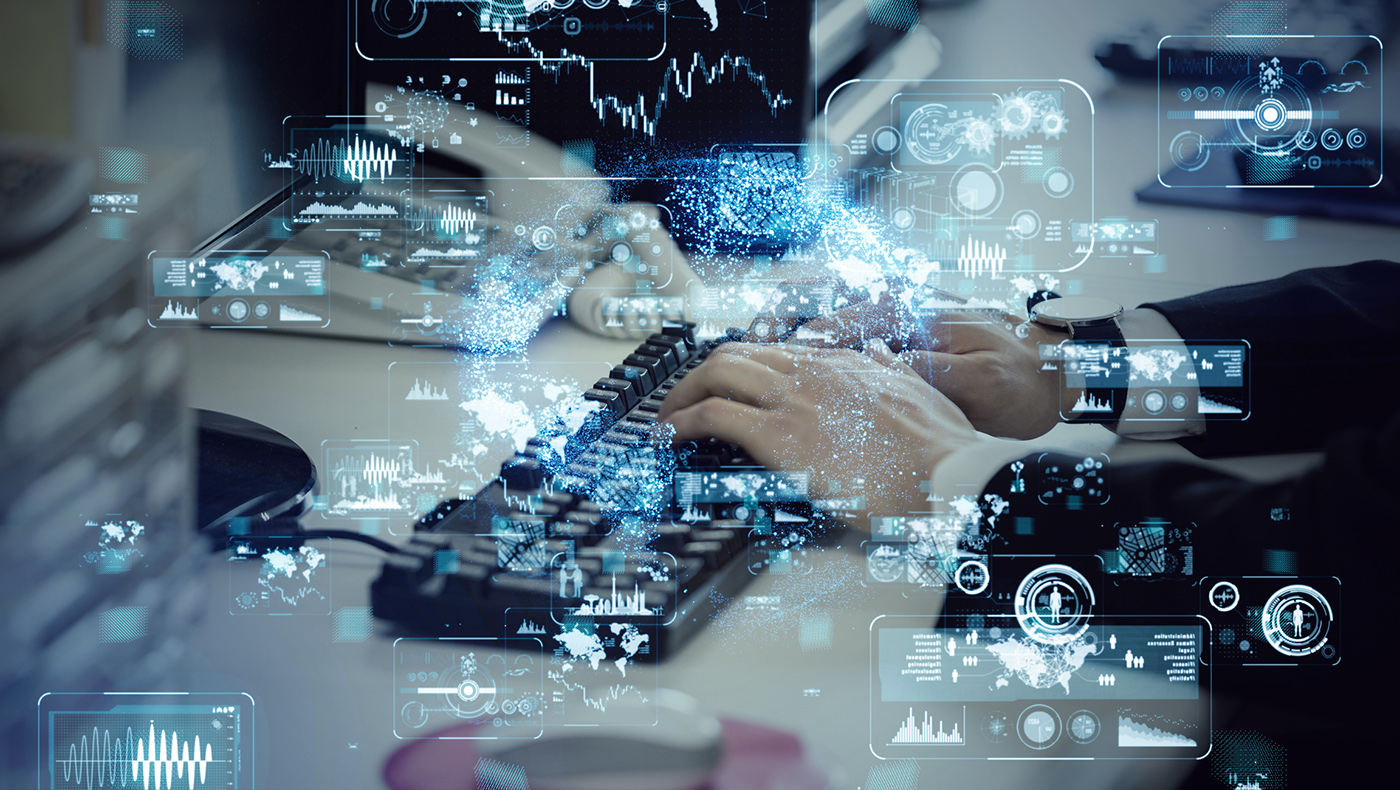
The International Data Corporation (IDC) estimates that digital transformation spending will reach $7.4 trillion in 2023, much of that spent in the manufacturing sector. Further, according to Manufacturing Global, 75% of large manufacturers are already investing in Industry 4.0/IoT technologies. OroCommerce, a provider of digital manufacturing solutions, helps companies improve their operational performance by:
- Utilizing machine learning to understand end-to-end processes and supply chain challenges
- Integrating manufacturing networks using tools such as enterprise resource planning, product information management, and e-procurement
- Deploying augmented reality (AR) to optimize factory operations and improve quality control
- Adopting digital tools that aid in integration of new business models and vendor and customer partnerships
“Quality and agility are keys to success in today’s manufacturing landscape. Companies must operate efficiently with smaller and more dispersed workforces to deliver shareholder value,” says Alan Stanfill, director of digital transformation with Gray Solutions, a Gray company. “To achieve this, companies need transparency and informed decision making at all levels of the organization, from manufacturing operations to the enterprise in a timely manner. This can be delivered today in ways that were unimaginable just a few years ago.”
On-Demand Manufacturing
With unstable supply chains, changing customer preferences, and product customization, on-demand manufacturing is growing in popularity as a way to satisfy these evolving needs at a variety of scales. Also known as custom manufacturing or cloud manufacturing, on-demand manufacturing relies on Industry 4.0/IoT technologies, typically linked through the cloud. Customers can upload details, plans, and other relevant data to an on-demand manufacturing platform, after which quotes and manufacturing parameters are locked in. Additive manufacturing/3D printing is a key technology that speeds up prototyping and production, controls costs, and is nimble enough to adjust for different production volumes.
Companies that have used an on-demand manufacturing platform report gains in quality (62%), transparency (61%), and speed (60%). “Following industry trends toward full customization and consumer-centrism, on-demand manufacturing offers scalable options for low-volume and mass production,” states Dave Evans, CEO of Fictiv, a digital manufacturing ecosystem company.
Digital Twins
Both traditional and on-demand manufacturing can benefit from the use of digital twins, which have the potential to transform manufacturing and maximize its efficiency, productivity, and profitability. “Grounded in the real-time reality of how a business actually operates, digital twins stretch the bounds of what’s possible by offering a virtual replica of any physical product, equipment asset, or supply chain,” says Sachin Lulla, an advanced manufacturing and mobility leader for EY.
Digital twins are only limited by the number of sensors utilized to create a digital replica of a product or system, or even an entire manufacturing ecosystem. With real-time digital threads, supply chains, factory floor setups, and product maintenance data, “organizations can create a digital twin for their entire business,” states IndustryWeek. This allows full-tilt simulation of everything, tracing the interconnectedness of every step in the chain and allowing manufacturers to experiment with changes and predict whether or not it’s worth adjusting a process.”
Dramatic Results
Improvements through digital transformation can be dramatic.
For example, BAE Systems, a British multinational defense and aerospace company, improved the efficiency of the assembly of complicated batteries by using augmented reality. The solution was a custom-designed software program that provided correct modeling of battery assembly instructions on a step-by-step, color-coded basis to maximize efficiency and minimize errors. This simple solution reduced assembly time by 50% and training time by more than 40%.
Even though 2022 is expected to be a more settled year than 2021, manufacturers have learned how important Industry 4.0/IoT is for surviving (or even thriving) during a crisis. The pandemic showed many companies that digital transformation isn’t only about reducing costs and increasing efficiencies, but also about embracing an agile mindset and maximizing revenue through unique competitive advantages.
“Digital transformation is an incremental process and choosing what data and processes to attack first is a key part of getting value from the investment,” says Brent Humphreys, principal digital strategist with Gray Solutions, a Gray company. “Choosing a partner experienced in implementing these technologies is a critical factor in success. A trusted advisor can help identify opportunities and build a road map for success.”
- Category:
- Industry
Some opinions expressed in this article may be those of a contributing author and not necessarily Gray.