Closing the Manufacturing Talent Gap, Part 1
Manufacturing executives baffled by the shortage of available workers with needed skills must continue to update their strategies for attracting, developing and retaining needed workers.
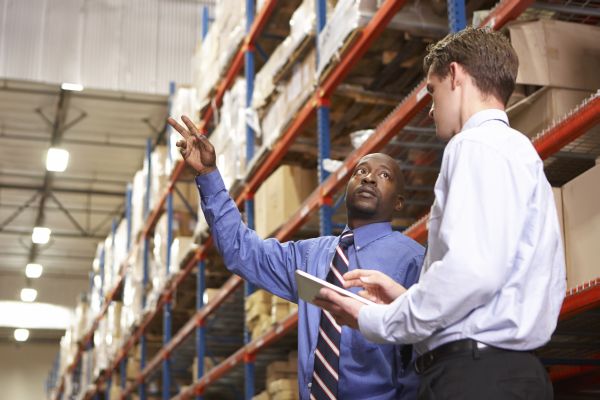
Manufacturing executives baffled by the shortage of available workers with needed skills must continue to update their strategies for attracting, developing and retaining needed workers. Failure to step up these initiatives threatens to crimp current organizational performance. It also undermines prospects for future competitiveness in fiercely-competitive global markets.
A study by Deloitte Consulting LLP and the Manufacturing Institute updated their Skills Gap report. It’s based on a study of manufacturing skills gaps and how they affect organizational performance. The study specifically looks at which manufacturing jobs are the most difficult to fill and which trends impact manufacturers, such as the speed and nature of change as well as the related skills requirements.
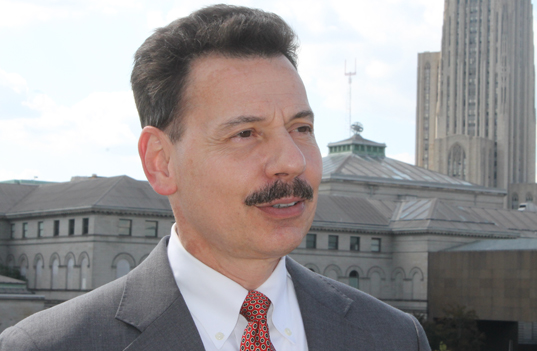
How well manufacturing leadership meets these challenges will shape the industry’s ability to drive and sustain significant economic gain. But, several hurdles must be overcome before this vision can become a reality. Speaking at an Aspen Institute meeting in Washington, Craig Giffi, Deloitte’s vice chairman and leader for U.S. Consumer & Industrial Products, cited several related gaps.
The perception gap is the first, and it undermines an organization’s best efforts to attract top talent. Corporations need to acknowledge and address the common perception that manufacturing serves up only low-paid, dirty jobs. To offset this perception, try sharing the good news about attractive manufacturing careers with schools and universities, community organizations, among other initiatives in your region. Invite students, local associations and your employees’ families to events that showcase what your company has to offer. While you’re at it, take a fresh look at your organization’s work environment, pay and benefits – how do they measure up against your competitors and other employers in your area?
Secondly, the education gap, marked by poor student performance in math, science and reading skills, dilutes potential job candidates’ capabilities for blueprint reading, quality performance improvement, etc. This can be improved if companies get involved with area educators in developing programs and coursework that can challenge and educate their future workers.
Thirdly, understand that, if you’re not investing in next-generation equipment and training, someone else will. Bridge the training gap to position your company a step ahead of the pack. Check out STEM (Science, Technology, Engineering and Mathematics) training programs available in your area or through various trade organizations, for example. Reach out to local colleges and universities as well as fellow manufacturers supporting or sponsoring STEM and other industry-focused training programs. Why reinvent the wheel, if others have already developed viable programs to provide needed skills?
Lastly, the policy gap presents complex challenges for manufacturing. Many senior manufacturing executives participate in studies and organizations aiming to revamp tax and regulatory reform, which could potentially mean changes going forward.
For more on Giffi’s explanation of these gaps, watch the presentation in full:
Beyond these gaps, a company’s own outdated perceptions can account for a dwindling pipeline of prospective new hires. It’s important to set aside yesterday’s stereotypes about the “ideal” job candidate and consider the pool of candidates currently in your region and your industry. How effectively have you sought women and minority employees, or military veterans? GE, the Manufacturing Institute and the National Association of Manufacturers (NAM) recently announced that 190 added manufacturers have joined the Get Skills to Work (GSTW) coalition. This initiative is ramping up new advanced manufacturing jobs prospects for veterans. Another often overlooked resource is the individuals who’ve been outsourced and whose skills may need updating.
Ultimately, your company is competing for customers against best-in-class companies around the world. To win the game, you need to review and refresh your strategies for sourcing, developing and retaining the talented folks who will make success happen for your organization.
Update: Find out more on this topic in Closing the Manufacturing Gap, Part 2.
Lea Tonkin has extensive experience as an editor and writer about manufacturing and business. She was the editor in chief of a national manufacturing trade association magazine and the group’s online newsletter, previously serving as the business editor for a chain of daily newspapers in the Chicago area and as an editor for plant engineering and purchasing management periodicals.
- Category:
- Industry
- Manufacturing
Some opinions expressed in this article may be those of a contributing author and not necessarily Gray.
Related News & Insights
Advanced Technology, Automation & Controls
Four Use Cases for AI's Growing Role in Manufacturing
Industry
November 25, 2024Data Centers
Gray Expands Reach with Dallas Office
Corporate News
November 14, 2024Manufacturing, Construction
The Evolving Role of Electric Vehicles in Sustainable Construction & Design
Industry
October 18, 2024