Building, Retrofitting, or Renovating a Plant? Remember the Workers
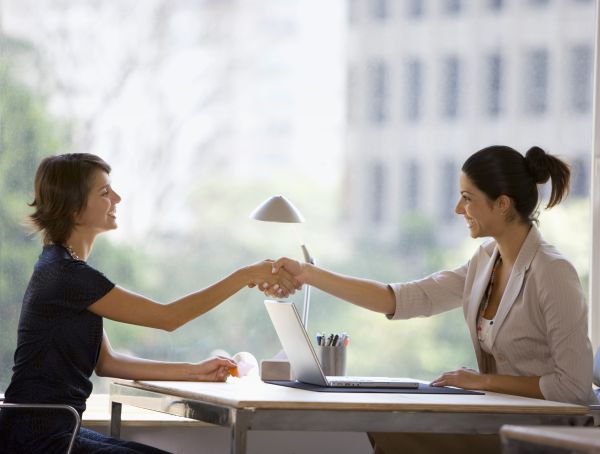
It pays to think about the people who will work there.
Evidence is mounting that there’s a business case for making the workspace work better for people. The right improvements in a building’s environment can be reflected in productivity and profits. Many efforts to improve employee comfort, however, are based on assumption and guesswork, when an analytical and data-based approach is required. Fortunately, as leading companies gain experience in employee-centered work environments, best practices are being quantified and the long term payoff demonstrated. Some of these principles are summarized in a new report, Health, Wellbeing, & Productivity in Offices: The Next Chapter for Green Building from the World Green Building Council (WGBC). While the focus of the report is on office environments, all manufacturing facilities have office space, breakout rooms, eating spaces, and public spaces. The principles also apply to factories.
Is there a business case for spending on worker comfort? Research is showing that when variables such as air quality, noise, lighting, and worker density are changed, people perform better (or worse) at decision-making and cognitive tasks. Even outside the lab, measurable reductions in absenteeism, medical costs, accident rates, and turnover have accompanied building environment improvements. When you consider that salaries, benefits, and other staff costs account for 90% of the typical business’s operating costs, the impact of even modest productivity gains are significant.
The WGBC report lays out a model and principles that help companies understand and plan a more people-centered work environment. It describes an integrated approach that considers financial, perceptual, and physical factors you can use in your own company. A first step is to create a cross-functional team with representation from the facilities, HR, and financial divisions. One thing that will help get a baseline is to take a look at readily available key metrics including absenteeism and turnover, revenue or production per employee, and the number and cost of safety and medical complaints. Then you can analyze them according to worksite — not department — to find differences in current facilities and target improvements. HR may already have good employee satisfaction and health and safety data, but you may need to know more about how employees feel about lighting and temperature conditions, what the effect of noise is on their work, how easy it is to move around the facility to accomplish tasks, and how they rate the appeal and amenities of their surroundings.
The physical data about the work site is easier to pin down than employees’ perceptions, but it’s important to capture the right details. You will probably need outside help for measuring variations in lighting in surroundings and at workstations, air circulation, CO2 and other pollutants, temperature, availability of windows, privacy, and the level of personal control. Most companies do not have such specialized engineering resources on staff, and an objective view is important. You also need experts in state-of-the-art equipment and controls you can build into your better place to work.
Interestingly, overall company environmental goal achievement and operational cost reductions come along with people-centered work site improvement. This report helps connect the dots between respect for people and their perceptions, physical and environmental factors in their workplaces, and improved profitability and productivity.
Whether you’re building or retrofitting, it pays to focus on people.
To dig deeper into the research behind the report, visit WGBC’s Research and References. Another relevant WGBC report is “The Business Case for Green Building: A Review of the Costs and Benefits for Developers, Investors and Occupants.”
As this report details, sustainable work environments are quickly becoming a priority for companies across the globe for reasons ranging from social responsibility to long term cost reductions. Learn more about how Gray accommodates its customer needs through sustainable design for green manufacturing here.
Karen Wilhelm has worked in the manufacturing industry for 25 years, and blogs at Lean Reflections, which has been named as one of the top ten lean blogs on the web.
Some opinions expressed in this article may be those of a contributing author and not necessarily Gray Construction.
- Category:
- Industry
- Manufacturing
Some opinions expressed in this article may be those of a contributing author and not necessarily Gray.
Related News & Insights
Manufacturing, Construction
The Evolving Role of Electric Vehicles in Sustainable Construction & Design
Industry
October 18, 2024Manufacturing
Sustainable Manufacturing Creates a Culture of Caring
Industry
Distribution, Advanced Automation
Shining a Light on the Lack of Fully Automated "Dark Factories"
Industry
September 27, 2024