Automation and AI to the Rescue
Automation and artificial intelligence (AI) have proven to be advantageous to industries, but the idea of robots taking jobs from humans felt threatening even before the catalyst of COVID entered our everyday vocabulary. Now, with the virus, many more companies are making efforts to adopt automation and AI to make their operations safer and more productive. Manufacturing was severely impacted as the pandemic swept around the globe, workers fell ill, and environments were deemed unsafe for human beings. For manufacturing, logistics, and fulfillment industries as well as their supply chains, people needed to be removed from the process. Turning to technology-based solutions helped keep the remaining humans safe and businesses running.
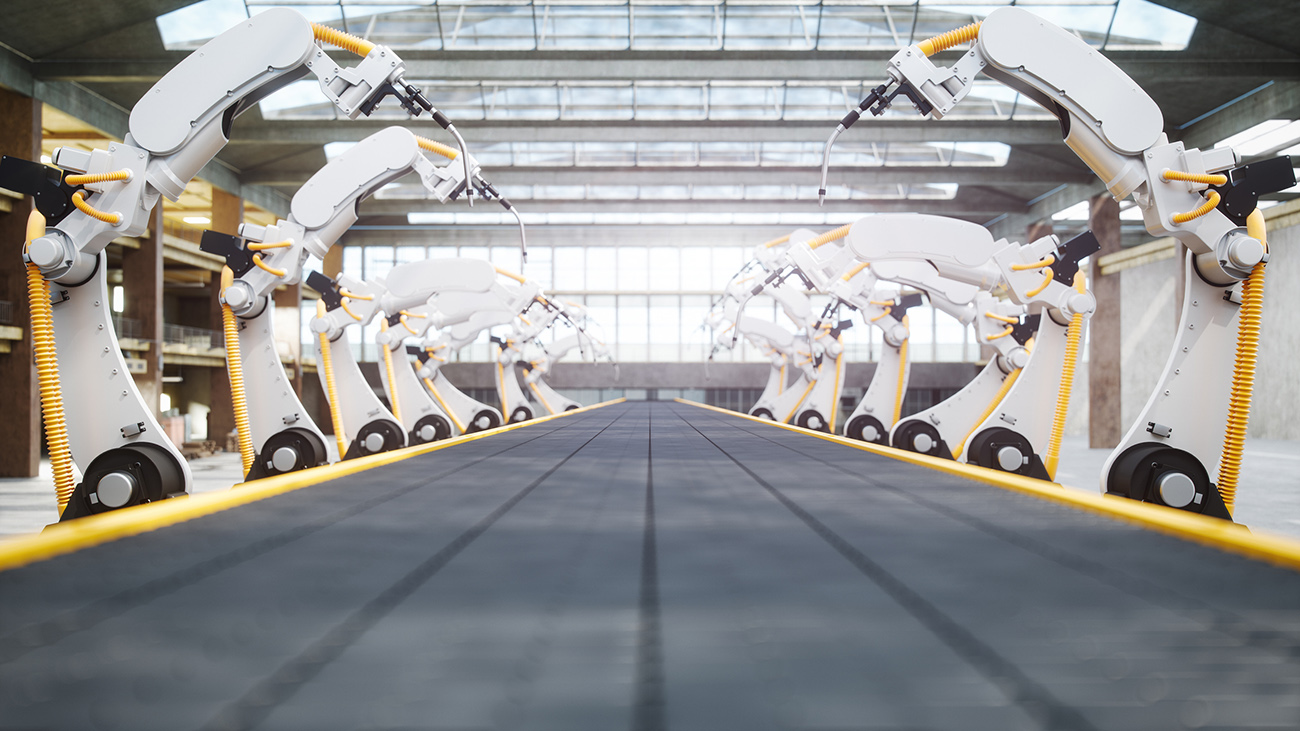
Automation allows machines or tools to operate more efficiently, freeing up workers to take on more challenging tasks. AI is the science behind making that automation intelligent and think for itself. Today, they go hand-in-hand when talking about advancements in manufacturing and how to better prepare for the future.
Below are several ways automation and AI are making manufacturing more efficient and crisis-proof in the coming years.
Predictive Maintenance: Routine maintenance on machines and their parts is costly in overhead and can eat up valuable time in production when a machine goes down. For example, downtime in the auto industry can cost up to $50,000 per minute.
AI-enhanced factories using predictive maintenance of industrial equipment can reduce annual maintenance costs and minimize expensive unplanned downtime. Smart sensors and AI software track wear and tear on machines and predict when maintenance is required. Lags in the production line can also be analyzed to improve efficiency, thus saving overall production costs.
Market Analysis and Forecasting: AI can analyze supply chain performance and market fluctuations, allowing companies to strategically plan products and updates. AI can analyze weather, risk management, political unrest, changes in consumer’s behavior (for example, a pandemic hits and online shopping increases), and other factors, allowing for faster supply chain adjustments. For example, Amazon’s “Hands Off the Wheel” initiative uses an algorithm to forecast demand, inventory, and even negotiations of prices with vendors.
Working with Robots and Cobots: Robots perform faster than humans, increasing efficiency and quality. They don’t need bathroom breaks or have responsibilities beyond work. Amazon, Alibaba, and Walmart are prime examples of companies that use robots in the fulfillment process to reduce redundant, tedious, and complicated tasks for humans.
Collaborative robots (cobots) work side by side with humans and rely on real-time data from vision and proximity sensors to learn about their surrounding environment and protect the humans working around them.
With COVID here to stay through 2021, as health experts caution, robots can be an effective solution for many companies until it is safe for their workers to return. They will be able to work in dangerous environments, assist with social distancing measures, or contribute when humans cannot complete that task by being physically in the building or from remote.
One robotics company getting more attention since the pandemic is UVD Robots, a Danish manufacturer of ultraviolet-light-disinfection robots. With AI technology, these robots can autonomously detect the virus and then kill it with UV light, effectively limiting the spread of coronaviruses without exposing hospital staff to the risk of infection.
Virtual and Augmented Reality (VR/AR): VR/AR are tools of engagement that allow humans to experience and share information about an environment without being there physically. Employees can connect remotely and work together on tasks or problems or work remotely on hazardous sites. Working through simulations of a new product with VR/AR can speed up manufacturing and reduce costs. VR technology also makes training more effective and reduces costs. Ford Motor Company uses FiVE, its VR lab, to help specialists inspect and test vehicles in different conditions, or collaborate together from separate locations throughout the globe.
Customer Service: Not responding to a vendor or customer promptly can lead to frustration and possible loss of revenue. AI can help analyze customer behavior and predict future needs or problems. AI collects and studies data on the clients’ purchases, conversations, and interactions with customer service, and much more. This data can then be used to craft the best personalized customer experience.
Many companies use chatbots to communicate with customers and create more humanistic experiences in their customer service departments. This helps resolve issues faster with short response times.
Cybersecurity: Now that more business is conducted online, cybersecurity is vital to keep transactions safe. Malware and hackers have their own AI, so industrial cybersecurity must go one step further to combat potential threats. Technology like “Generative Unsupervised A” is being used daily – this is an adaptive algorithm that will detect abnormalities from data, flag them, and learn from them to thwart software vulnerability (zero-day) attacks. AI gathers information and analyses that data from various research of sources. IBM’s “Watson” algorithm grows stronger and faster as it learns to pinpoint threats, reducing the time it takes to respond to a cyber-attack.
Smart Factories Are the New Factories
Combining AI, automation, VR/AR, 3D printing, and other Internet of Things (IoT) technologies make manufacturing operations “smarter.”
Siemens’ plant in Amberg, Germany, is an excellent example of a smart factory at work. MindSphere, Siemens’ Internet of Things (IoT) operating system, analyzes and stores operational data and allows for online monitoring of globally distributed machine tools, industrial robots, or industrial equipment. Siemens engineers have created an AI-driven, two-armed robot that is capable of building prototypes of products without needing to be programmed. Each arm functions autonomously but fluidly with the other.
“Siemens is focusing on reshaping processes with digitalization, both for its industrial enterprises and its production operations,” says Klaus Helmrich, CEO of Siemens Digital Industries. “Digital transformation will be critical for the manufacturing industries to increase productivity, flexibility and accelerate innovation, so companies must come together in new ways to enable the digital enterprise.”
Pulling the Positive from the Pandemic
Automation and AI were here before COVID, but only used by those pushing the envelope. COVID, however, has become a powerful incentive to adopt these and other IoT technologies as a necessity to stay in business and be better prepared for future disruptions.
- Category:
- Industry
- Construction
- Manufacturing
Some opinions expressed in this article may be those of a contributing author and not necessarily Gray.
Related News & Insights
Advanced Technology, Automation & Controls
Four Use Cases for AI's Growing Role in Manufacturing
Industry
November 25, 2024Data Centers
Gray Expands Reach with Dallas Office
Corporate News
November 14, 2024Manufacturing, Construction
The Evolving Role of Electric Vehicles in Sustainable Construction & Design
Industry
October 18, 2024