A Fresh Approach to Strengthen the New Collar Workforce
By 2025, the U.S. manufacturing industry is expected to have about two million unfilled manufacturing jobs because companies will not be able to find workers with the higher-tech skills required to operate advanced manufacturing equipment. This is already a critical situation for many companies, especially as Industry 4.0 and Internet of Things technologies move to the forefront. For example, additive manufacturing is a rapidly expanding field that is in desperate need of skilled operators and technicians.
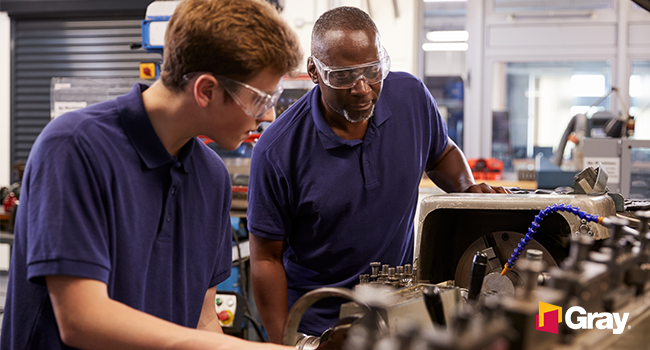
By 2025, the U.S. manufacturing industry is expected to have about two million unfilled manufacturing jobs because companies will not be able to find workers with the higher-tech skills required to operate advanced manufacturing equipment. This is already a critical situation for many companies, especially as Industry 4.0 and Internet of Things technologies move to the forefront. For example, additive manufacturing is a rapidly expanding field that is in desperate need of skilled operators and technicians.
To ease this looming job challenge, the manufacturing industry must create a pipeline of workers who have advanced technology skills. Gaining these skills typically requires one or two years of post-secondary education or training. These workers represent the “new collar” workforce, because they require more specialized technology training compared to traditional “blue collar” positions.
Fab Lab Hub, an organization founded by Sarah Boisvert to train the new-collar workforce, has partnered with America Makes, a national additive manufacturing research organization, to create a “digital badge” program that trains employees in the high-demand jobs of operating additive manufacturing equipment such as fused deposition modeling (FDM) and stereolithography (SLA).
A Variety of Topics
The Fab Lab Hub-America Makes digital badge partnership is based on the Open Badge concept that was originally developed by Mozilla. The Fab Lab Hub-America Makes program includes:
-
- Design for 3D printing
-
- Introduction to CAD design
-
- Fundamentals of SLA 3D printing
-
- Troubleshooting FDM 3D printers
-
- Laser safety in manufacturing
Boisvert is especially enthusiastic about the digital badge format, because it also helps workers sharpen their critical-thinking skills.
“In researching my book, The New-Collar Workforce, I learned that 95 percent of manufacturers were looking for employees with strong problem-solving skills, above all other capabilities,” says Boisvert. “The digital badge platform allows us to document problem-solving used in the required project via a portfolio that contains photos, videos and essays. It’s an in-depth record of the critical-thinking process, well beyond passing a test.”
Improving New-Collar Skills Nationwide
Training for badges typically runs from four to eight weeks, with an average cost of $250 and $50-$100 in lab fees. Badges can also be stacked to create “master” badges for FDM and SLA operators and technicians.
Facilities for training will include other fab labs (all members of the larger Fab Lab Network) and educational institutions across the country—locations include Detroit, Cleveland, Baltimore, Boston, Pittsburgh, Tulsa, Denver, Santa Fe, Oakland and El Paso.
A pilot launch of Additive Manufacturing Digital Badge program will be conducted before it is made available to a larger network of about 250 fab labs in North America and other partners, including colleges and universities and K-12 school systems.
Making a Difference
Boisvert hopes the digital badge program increases public awareness of new-collar jobs and spark interest in manufacturing careers. For example, she says, “the short duration it takes to earn the badge, and the low cost, allows someone to try a manufacturing job to see if it’s a good career path before committing to a long program.” Digital badges can also provide a pathway to a college degree or other post-secondary certification program.
Industry support is crucial to this effort and manufacturers can join the North American Digital Fabrication Alliance to support the digital badge program.
“Our ultimate goal is to create a ‘LinkedIn for New-Collar Workers’ group so employers can easily find the staff with skills they need,” says Boisvert.
Because education is at a crossroads and facing declining enrollments, she notes, “we must provide affordable options that integrate with today’s technology-driven, fast-paced landscape. Digital badges for new-collar skills will hopefully provide an engaging pathway to jobs for workers who didn’t realize some of these careers are available, or who are interested in pursuing STEM [science, technology, engineering, math] degrees to gain a higher level of proficiency and understanding.”
- Category:
- Industry
- Opinion
- Construction
- Manufacturing
Some opinions expressed in this article may be those of a contributing author and not necessarily Gray.
Related News & Insights
“New Collar” Workers Are the Future of Manufacturing
Industry, Opinion
Manufacturing, Digital
How Artificial Intelligence Improves Worker Performance
Industry, Opinion
Advanced Technology, Automation & Controls
Four Use Cases for AI's Growing Role in Manufacturing
Industry
November 25, 2024