8 Lessons that Flint City Managers Can Learn from Manufacturing
By now, everyone knows that Flint’s emergency manager decided to save money by taking water from the Flint River instead of buying Lake Huron water from Detroit.
The result of the poorly managed change was lead and other contaminants in the water, causing permanent harm to Flint’s children.
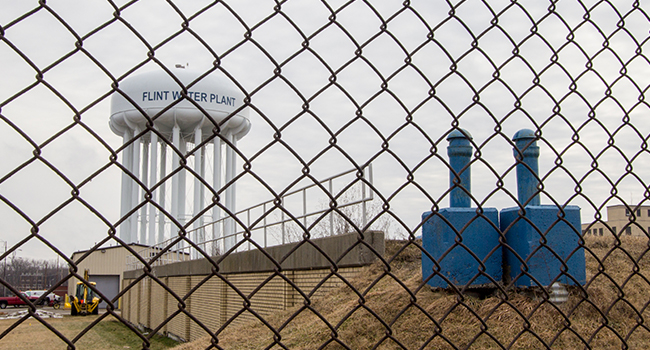
Could good manufacturing principles have prevented this disaster?
If the drive to cut water supply costs had followed world-class manufacturing principles, could this disaster have been avoided? Let’s take a look at how they might have helped:
- Avoid focusing only on costs—and avoid using dramatic projected cost savings for grandstanding and publicity.
- Understand the process thoroughly before changing it. Map and document the system as-is. Stabilize the system and its inputs and processes, then start looking for improvements. Flint might have found enough waste in their water delivery process that the big change might have not been necessary.
- Practice standardization. Flint had to adopt new water treatment processes that were formerly been Detroit’s responsibility. One standard process for preventing corrosion was omitted.
- Put safety first. Throughout the decisions, construction, change, and assessing results, the safety of Flint residents must not have been as important as getting the project done. When evidence of trouble appeared, the water department did not act to keep its customers safe.
- Make sure you have good data. Were accurate test results submitted to the EPA and the Michigan DEQ? There’s some evidence that they were compromised by improper sampling, and by deviating from standard testing processes.
- Don’t hide problems. If water quality test results were manipulated before they went to the EPA and Michigan’s Department of Environmental Quality (DEQ). In turn, those agencies ignored evidence from customers and third party testers.
- Find defects and correct root causes. The water delivered was defective. At the same time as it caused visible skin rashes, it silently raised blood lead and iron levels in residents. It was toxic. One root cause soon became obvious—standard corrosion prevention treatments were not being used. Instead of immediate corrective action, it took public pressure to get the city to reveal the problem and implement the process.
- Increase customer focus. A customer-focused organization would have as its mission to deliver clean, safe water to residents. Instead of being helped when they complained about contamination, customers were brushed off. It took the persistence of one mother and a lone EPA investigator to bring the problem to light—with the help of the press.
Ironically, a new water intake from Lake Huron has been under construction and will be completed this year. Using Flint River water was only going to be a temporary stopgap. Pushing for quick cost savings was a fatal mistake. Had the city just continued to pay for Detroit water for two more years, it would have avoided the entire debacle.
Karen Wilhelm has worked in the manufacturing industry for 25 years, and blogs at Lean Reflections, which has been named as one of the top ten lean blogs on the web.
- Category:
- Industry
- Manufacturing
Some opinions expressed in this article may be those of a contributing author and not necessarily Gray.
Related News & Insights
Advanced Technology, Automation & Controls
Four Use Cases for AI's Growing Role in Manufacturing
Industry
November 25, 2024Data Centers
Gray Expands Reach with Dallas Office
Corporate News
November 14, 2024Manufacturing, Construction
The Evolving Role of Electric Vehicles in Sustainable Construction & Design
Industry
October 18, 2024