3 Manufacturing Technology Trends to Watch in 2017
What is the simplest and most direct definition of manufacturing you can envision? Likely it would be taking a raw material and processing it into a useful component or end product. Whether a paper clip or a Porsche, manufacturing is a process that adds value, consumes energy, transforms raw materials, and creates wealth.
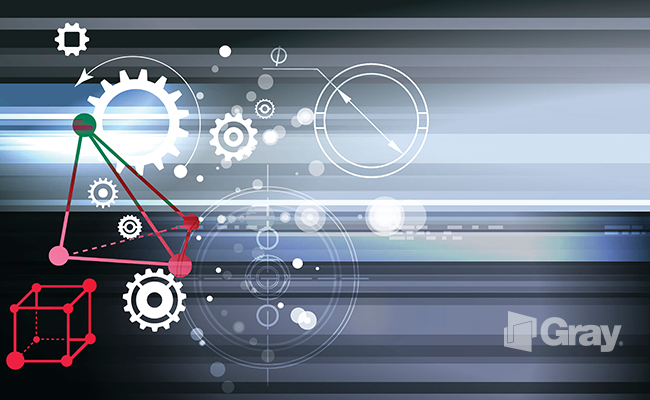
New tools, techniques, and infrastructure are driving evolutionary changes.
Manufacturing is also undergoing dynamic change at a rate that even existing practitioners would find amazing and that previous generations would not even recognize. Consider the following trends defining manufacturing now and for the future:
1) Computing Power
From increasingly sophisticated CAD/CAM packages driving computer-controlled machine tools to enterprise-wide planning packages, manufacturing is a digital, data-driven process. With computing becoming faster, more powerful, and cheaper, this is transforming manufacturing from a linear, beginning-to-end process to an upward spiral where plant-floor data is collected, analyzed, and repurposed to improve efficiencies and eliminate errors.
This is not limited to the production process, but is also increasingly taking in purchasing incoming materials, shipping and logistics, quality control and inspection, and obtaining and setting up tooling for your equipment. The Machining Cloud is a consortium of dozens of worldwide tooling suppliers that have digitized their catalogs and all related setup, speeds, and troubleshooting data, and have made all this data downloadable to smart devices. Where setup people had to look up all parts and assemblies in catalogs and hope they had everything covered, cloud-based tool and setup data is saving hours if not days in setup time while assuring users they are getting the right setup for the right job.
2. 3D Printing
The concept of transforming raw material to finished product applies to 3D printing, but the concept of printing parts from metal powders or high-performance resins as opposed to chipping away at blocks or bars of metal is redefining manufacturing.
Consulting firm IDC forecasts that global spending on 3D printers, related materials and services is expected to total $13.2 billion in 2016, and grow to over $28 billion in 2020. More research is saying 3D printing will experience 30% compound annual growth and reach $30 billion by 2022. In its April 2016 study, “3D Printing Comes of Age in US Industrial Manufacturing,” Price Waterhouse Coopers (PWC) says compared to two years ago, more manufacturers (52% this year compared to 38% in 2014) expect 3D printing to be used in high-volume production in the next three to five years.
Currently making inroads in prototyping and low-volume production, 3D printing is also reshaping the concept of the factory. Large manufacturing plants for high-volume components and products, such as in automotive, are not going away, but for spare parts or small lots of critical parts, there could be a factory in every neighborhood.
UPS, for example, has announced it is installing 3D printers in more than 60 UPS stores, tying 3D printing into its logistics expertise to bring needed parts faster to more customers. “By building this disruptive technology into our supply chain models, we also bring new value to our manufacturing customers of all sizes,” said Stan Deans, president, UPS Global Distribution & Logistics. “Additive manufacturing technology is still developing rapidly so ‘manufacturing as a service’ is a smart approach for many companies.”
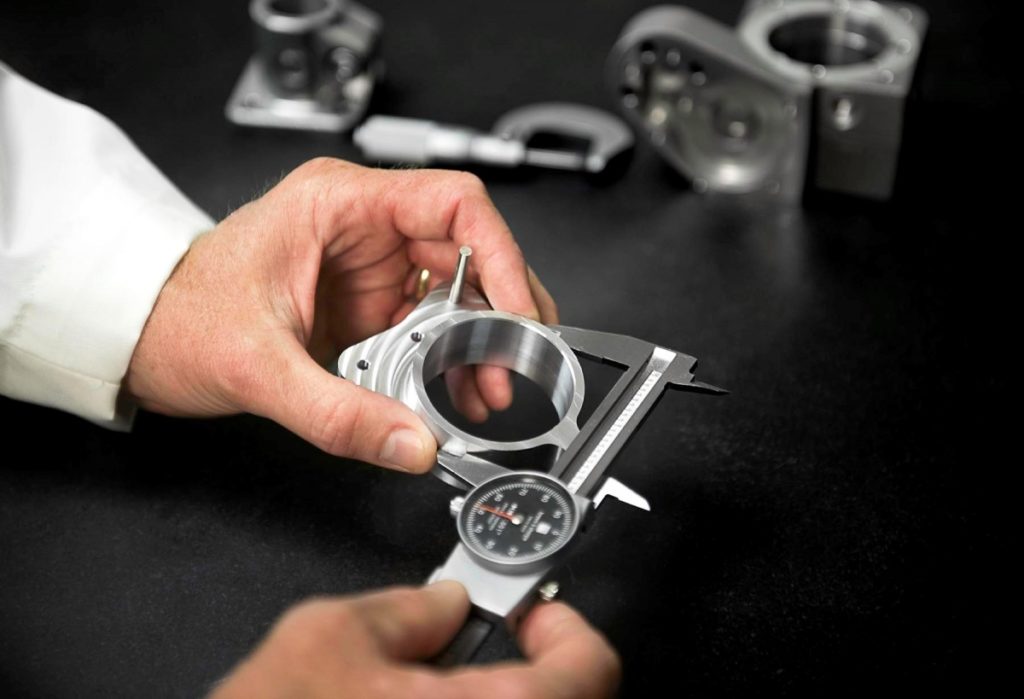
3. Sustainability
While digital data and breakthrough methods of making things will continue to reshape manufacturing, the process itself is becoming not only safer, but cleaner. In January 2017, Procter & Gamble vowed to eliminate all manufacturing waste from more than 100 plants around the world by sometime in 2020.
The Cincinnati-based maker of Tide detergent (NYSE: PG) plans to increase its investment in recycling to eliminate or re-use about 650,000 metric tons of waste that would typically go to landfills. That would be equivalent to the weight of nearly 350,000 mid-size cars, P&G stated.
P&G said it will achieve its zero-waste goals by ensuring all incoming materials are either converted into finished product, recycled internally or externally, or re-used in other ways through partnerships.
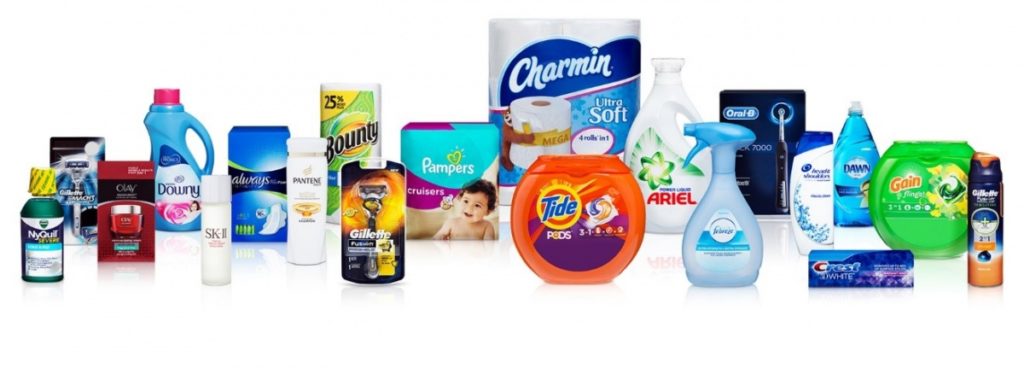
For example, at P&G’s plant in Bath Township, Ohio, liquid waste from products such as Tide and Gain detergents are being converted to alternative fuel to power vehicles. In addition, non-recyclable plastic laminate materials from P&G plants in Mandideep and Baddi in India are shredded and pressed into low-cost building panels.
Our parents or grandparents may have thought of factory work as dirty, dull, or dangerous, but today’s plants are cleaner, quieter, and more demanding of an integrated and inquisitive approach from designers and workers. Here’s to a bright future.
- Category:
- Industry
- Manufacturing
Some opinions expressed in this article may be those of a contributing author and not necessarily Gray.