Technology Is the Future of Manufacturing
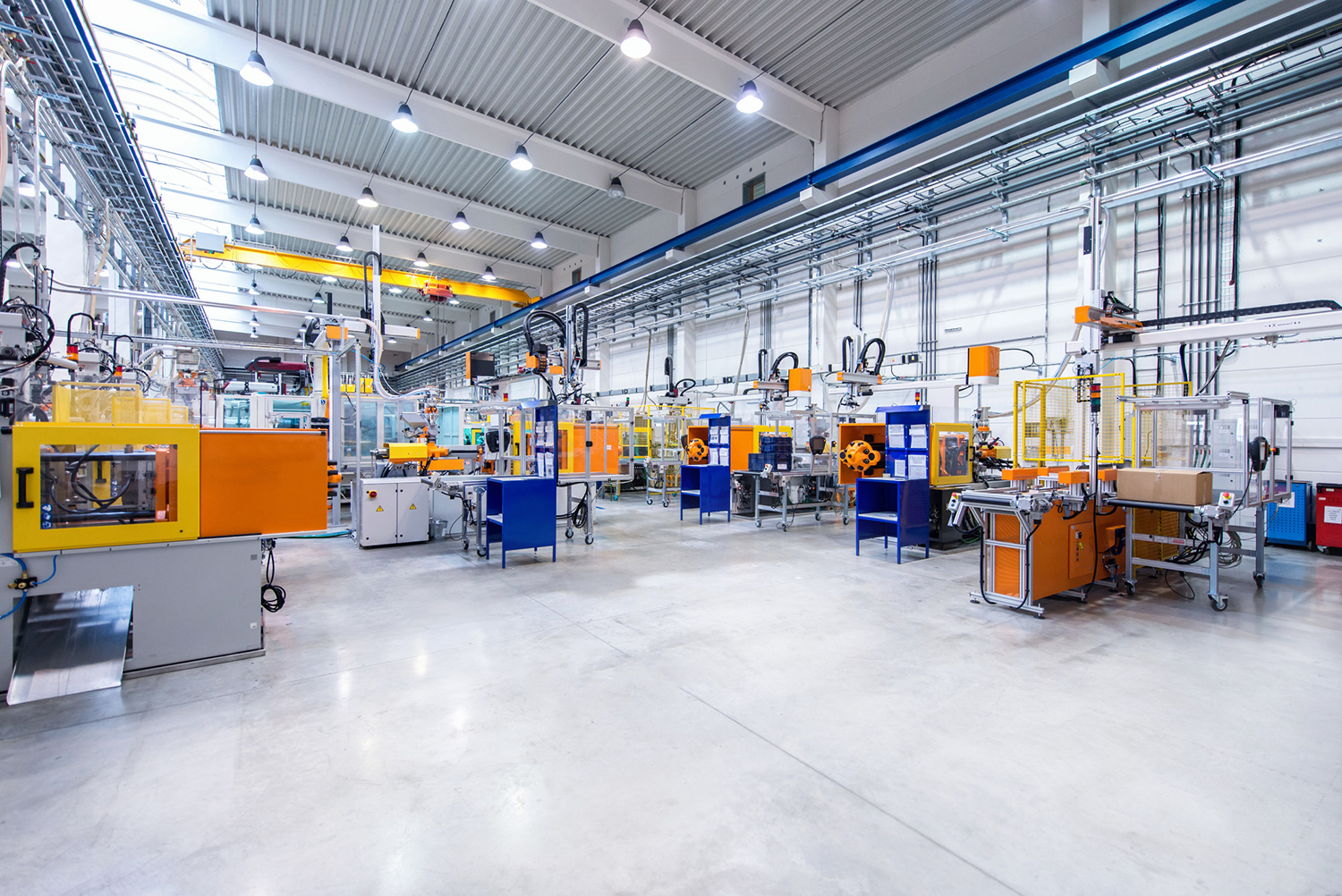
Global manufacturing continues to evolve rapidly, creating new challenges and opportunities for engineers. For leaders, keeping up with technology and management trends typically requires careful evaluation, capital investment, and embracing new ways of doing business to stay competitive. As older employees retire, changing workforce demographics will shape a new wave of leaders and workers, with different needs. Manufacturers must learn how to utilize Industry 4.0 and the Internet of Things technologies to compete effectively, with a focus on speed and personalization of products.
Below are four key business considerations for manufacturing leaders as they move into an Industry 4.0 world.
1. LEADERSHIP.
What foresight does a company need to prepare for new leadership, as older CEOs and other executives retire? “The next generation of leadership will be a reflection of the next generation of customers,” says Jignasha Amin Grooms, chief human resources officer at Epicor, a manufacturing and distribution software company. “Organizations in every industry need to prepare future leaders to be business-savvy, agile, and innovative in order to be successful in an environment where customers have limitless choices.”
Experience, technology knowledge, collaboration, and interaction with others are all critical skills for new leaders to have—especially for understanding new generations of workers and how to motivate them. “Knowing the business is important, but to challenge existing paradigms, you also often have to consider introducing new talent from outside your organization and your industry,” Grooms adds.
2. Workforce.
More workers are retiring than entering the manufacturing workforce. In fact, it has been predicted that two million manufacturing jobs will remain unfilled by 2025. New leaders must be committed to developing capable workers by providing the tech skills they need, creating the “new collar workforce.” They must also learn how to motivate workers in order to retain them—younger generations of workers want more responsibility and advancement, using innovative technology tools and methods. HR departments need to acknowledge that these workers will move on eventually if they are not motivated and do not have meaningful opportunities to expand their skill sets.
“Talk to your managers and supervisors about the talent they manage and use behavioral interviewing to bring in great, high-potential future leaders,” adds Grooms. “Tools such as 9 box grids help identify who the up-and-coming rock stars are within the organization.”
3. Embrace new technologies.
In an increasingly competitive global economy, manufacturers are keen on maintaining the strongest profit margins they can. This has been a challenge in recent years as the industry average EBITDA margin (earnings before interest, tax, depreciation, and amortization as a percentage of total revenue) continues to decline, from 11.2% in 2015 to 8.6% in 2018. This requires more efficient use of expensive fixed assets and staying ahead of the curve on new technology and business models. Increasing competitiveness means keeping pace with high-impact, disruptive technologies such as additive manufacturing, advanced materials, data analytics, automation, and robotics. Cloud-based software-as-a-service (SaaS) especially stands out as a solution for improving machine utilization and productivity, skills shortage, throughput rate, and speed to market.
Ultimately, the type of technology adoption depends on what consumers want and how fast they want them. “You’ll see more products driven by customers’ individual needs and specifications produced in a customer-driven factory, not a product-driven factory,” observes Scott Price, chief strategy and transformation officer for UPS.
Artificial intelligence (AI) is definitely a game-changing technology. AI algorithms are used to make complex decisions, often in real time on the factory floor. AI and machine learning will steadily improve what automation and robots can do, from customizing products to meet individual customer requirements to working side-by-side with humans. “For example, AI is enabling robots to take instructions from humans, including novel instructions not anticipated in the robot’s original programming,” states design and engineering software company Autodesk.
4. Supply chain management.
According to Bain, 70% of executives believe digital innovation will improve their supply chains during the next five years by improving service levels, delivery efficiency, supply chain transparency and traceability, lead times, and warehouse productivity, as well as financing decisions, inventory, maintenance of equipment, and energy consumption.
Many of these improvements are software-driven, providing better real-time management, and can be integrated into existing enterprise management and customer relationship management software systems. AI algorithms can determine patterns of demand for products over time and across geographic markets, even accounting for geopolitical incidents.
Samuel Roscoe, senior lecturer in operations management and research leader for the Supply Chain 4.0 Hub at the University of Sussex Business School, indicates that “AI and the predictive power of big data analytics enables companies to anticipate what customers will purchase, before they know themselves,” he says. “Blockchain is also enhancing transparency and traceability across multiple tiers of the supply chain, prompting companies to rethink their sourcing strategies when nefarious raw material extraction processes are identified.”
Moving Forward
Factories of the future will be more predictive and autonomous, relying on Industry 4.0 technologies and software and cloud-based SaaS programs. The digital supply chain will “become the digital and physical thread connecting products from birth to death, and then to a new life through recycling,” says Price. “Leaders will tap into new business models, using Industry 4.0 to create fundamentally better solutions for people around the world.”
For many companies, the speed of change feels daunting.
Price advises that, to integrate new business models built around Industry 4.0, most manufacturers will need to upgrade their skill sets. “For many, it will not only be a matter of learning what’s new but also un-learning what’s old,” Price adds. “Consumers bring none of that baggage to the revolution. They want only what’s better, faster, cheaper, and they don’t care what legacy processes are transformed in the process. Innovation will help manufacturers bridge the gap.”
Some opinions expressed in this article may be those of a contributing author and not necessarily Gray.
Related News & Insights
Distribution, Specialty Equipment
Equipment Manufacturing Trends for 2025
Industry, Opinion
Advanced Technology, Specialty Equipment
How an Equipment Design-Build Partner Benefits Your Business
Industry, Opinion
Manufacturing
Gray, UBE C1 Chemicals America, Inc., and Cornerstone Energy Park Celebrate Groundbreaking for New Manufacturing Facility
Corporate News
February 26, 2025