Manufacturing Convergence and the Industrial Internet of Things
Complexities reducing, opportunities expanding
Manufacturing has always been a process — raw material at one end, finished product at the other. But more and more, manufacturing is the site where many processes are converging: computer-aided design (CAD), process simulation, the actual machining processes plus machine tool monitoring and adjusting, plant and shipping logistics and much more, all made possible over the Internet, specifically the Industrial Internet of Things (IIoT).
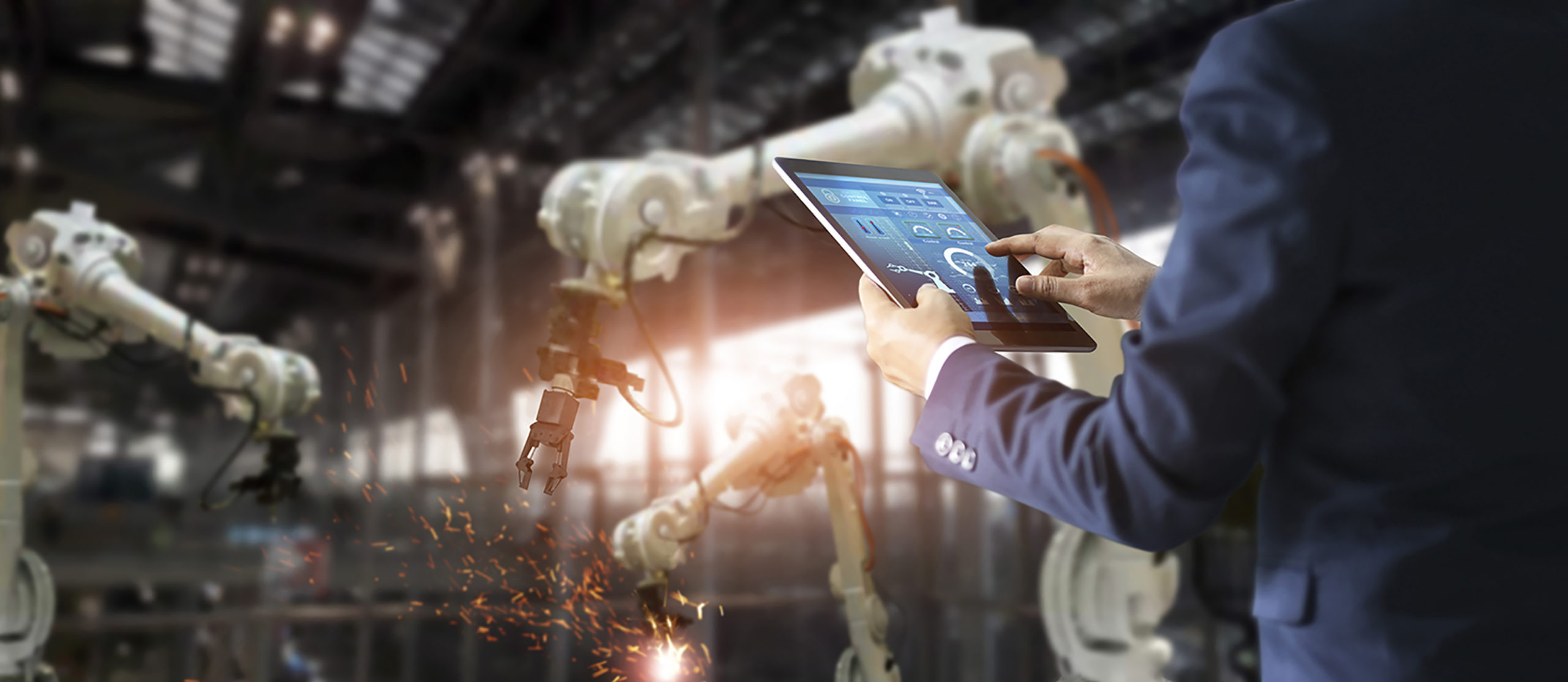
Two main concepts help frame thinking about the IIoT implementation:Improving plant operations through all these connectable controllers, sensors and other industrial devices is clearly the biggest potential of adopting the IIoT programs. Other targets include better demand forecasting, inventory optimization and improved regulatory compliance. This is a global phenomenon. Research organizations, universities and technology providers around the world recognize that manufacturing has billions of connectible devices, yet IIoT strategies are still emerging. Survey results from a 2017 international IIoT conference revealed 80 percent believed there is no corporate vision or strategy on digitalization, while only 4 percent reported both vision and execution plans are in place.
- It’s not one size fits all. Experts say the market for defining the IIoT strategy and adoption is driven by individual use scenarios.
- Budget numbers are growing. Estimates show the IIoT-related spending will reach $300 billion by 2020, but not all IIoT segments will grow equally. International Data Corporation (IDC), the premier global research group, has found the market for the IIoT applications and services will increase six-fold, from $10 billion to $60 billion, by 2020 specifically due to user customization. Connected things in industry, including controllers, sensors and microprocessors will double in market size from $20 billion to an estimated $50 billion but will face commodity headwinds.
Draw Your Roadmap
“Despite producing the most data, manufacturing is ranked last in digital transformation efforts,” confirms Graham Immerman, director of marketing, MachineMetrics, an IIoT platform provider. “Compared to all other global industries, manufacturing is still caught in a state of reactivity. Lacking a roadmap, the result is hesitancy.”
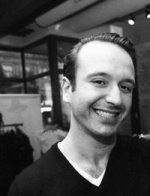
Following an IIoT commitment, the steps that manufacturers should take to digitally transform their operations become clear, says Joe Whyte, director of serialization and connected enterprise solutions at Rockwell Automation.
Step #1: Connectivity
Digital transformations cannot occur overnight. The journey begins with assessing each plant’s current network architecture and embracing Ethernet as the core infrastructure standard. Once the current state is understood, a plan should be developed to connect every smart device that can generate data to build one cohesive system over time.
Step #2: Security
With connectivity comes the need for an in-depth security strategy that protects a company’s data and ensures that only those who are authorized can access it.
Step #3: Collect Data
When collected, contextualized and analyzed, data delivers value to stakeholders at every level. However, for digital transformations to be cost-effective, a scalable data collection and storage strategy needs to be developed. Data should be collected, stored and analyzed as close to the source of the data as possible to derive immediate and maximum value from the data.
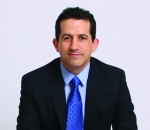
Step #4: Analyze
A scalable analytics strategy should be deployed to deliver value to every stakeholder at every level. Collecting all plant floor data and sending it to an enterprise cloud environment for storage and analysis is cost-prohibitive from a storage perspective and resource-intensive from a data science perspective. Collecting data and applying unique operational expertise and machine learning delivers production-layer insights. Such analyses provide real value to every stakeholder at every level of a manufacturing operation.
“Transformation requires buy-in from the front office and on the shop floor, but it also requires internal leadership,” says Immerman. “It’s critical for manufacturers to recognize the important role organizational attributes play in long-term project success and begin discussions about increasing the odds of project success by evaluating organizational gaps.”
Fastenal, a manufacturer of fasteners, tools and industrial supplies based in Winona, Minn., began investigating an IIoT solution in 2016. “The objective was to better understand their downtime, machine utilization, quality issues and to embrace the IIoT technology for production efficiency and process improvement,” Immerman says.
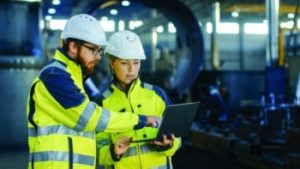
Data collection and analysis plus connectivity over the IIot means your data is working for you, not the other way around.The company chose MachineMetrics to monitor 11 Swiss machines and three turning centers. They installed monitors in their manufacturing plants so that both operators and managers could understand what was happening. Tablets were also made available for gathering feedback from operators immediately when necessary. In the three months since implementing MachineMetrics, the company ran 305 hours faster than the previous three months. “At this rate, we have been able to boost production by over 100 hours each month. It’s the same as adding over two weeks to each month.”
Some opinions expressed in this article may be those of a contributing author and not necessarily Gray.
Related News & Insights
Food & Beverage, Construction
Enabling the IIoT: Collecting Data, Eliminating Pain Points
GrayWay, Industry
The Positive Disruption of the Internet of Things on Distribution Systems
Industry, Opinion
Manufacturing
Autonomous Vehicles Remaking Automotive Manufacturing
Industry, Opinion