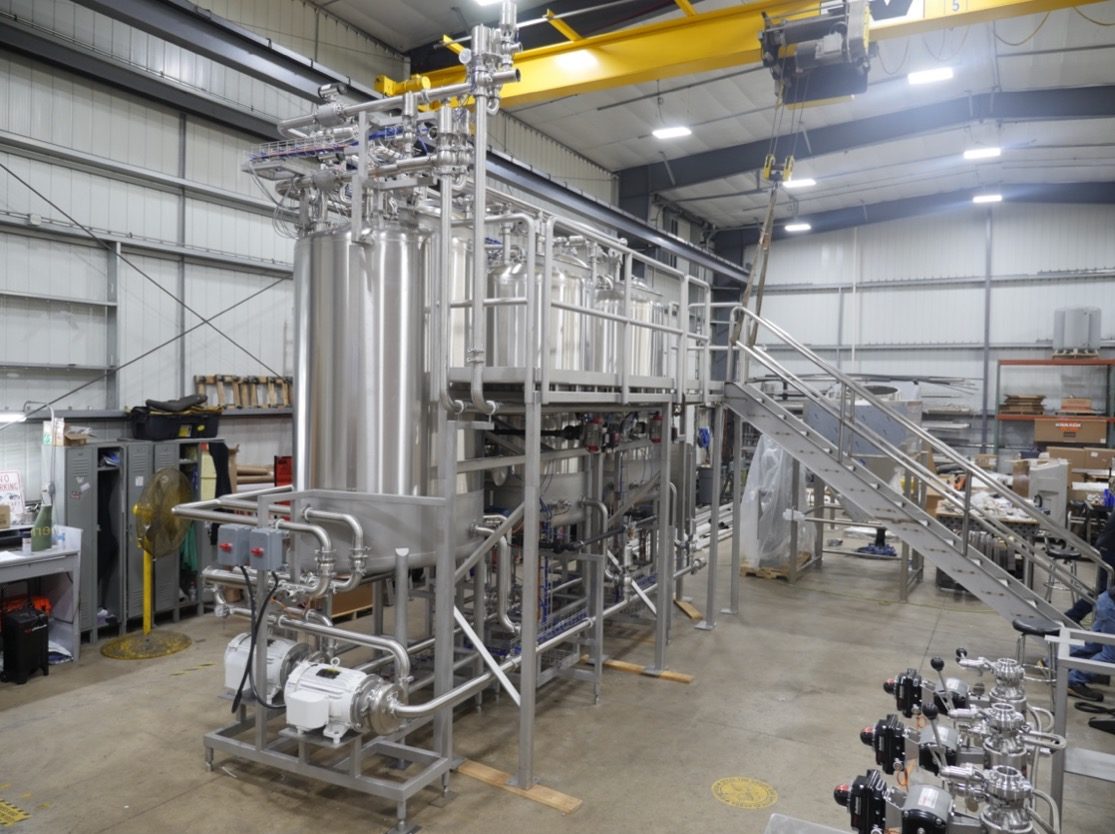
insights
Tips & Tricks to Specifying Clean-in-Place (CIP) Systems
Manually cleaning tanks, lines, blenders, mixers, and other process equipment can be a costly and time-consuming operation. Yet, it is critical to maintain sanitation standards to avoid product recalls and meet all local and federal regulations. Many companies explore installing Clean-in-Place (CIP) systems, which takes the burden off the operator and enhances sanitation methods, but may not know where to start. There is a lot to consider when thinking about installing a system – the proper sizing of tanks, the flow rates, heating methods, etc. – so it can be worth partnering with a trusted equipment integration provider to make sure your investment is worth the return.
Let’s review some considerations when planning a CIP system:
Product Type
The type of product that interacts with the process equipment plays a key role in the flow rate for the CIP system and which chemicals are required for the cleaning process. Some conditions may be described as heavy (dried carbohydrates, ground meat, cheese), moderate (wet carbohydrates, fats/oils, wet fruit material), or light (dry ingredients, wet vegetable or meat product, non-food material).
Equipment Needs
To fully specify the CIP system, all equipment needs to be identified upfront. This may include tanks, lines, fillers, mixers, coaters, spray dryers, blenders, ovens, and freezers. The size of the tanks and lines is also important when specifying the CIP system. This all contributes to the flow rate and pressures the system needs to support. The type of tank is dependent on industry, with ASME tanks frequently used in the pharmaceutical industry while atmospheric tanks and insulated tanks are better suited for other industries.
Cleaning Frequency
Every application will have a different cleaning schedule. This may depend on regulations, the type of product, or different recipe batches. CIP systems can clean every 12 hours, every week, every month – whatever your application needs. Knowing how often you want your process equipment cleaned, along with any limitations on cleaning time, determines the type of CIP system.
Heating Elements
Based on the utilities available in the space (steam, electrical, natural gas), a heating media transfers heat from one medium to another. Many facilities already have standardized methods for how they heat media, typically heat exchangers. Other methods may include direct steam injection, electric heaters, submersed plates, or steam coils.
Valves
The specified valves for the CIP system are customized for the industry requirements. When there are not stringent guidelines, butterfly and ball valves are often used to reduce cost. Pharmaceutical companies typically use diaphragm valves while dairy products need open yoke valves for 3A requirements. Additional valving features may include air-blow, throttling, burst rinse, drain valve, and recirculation for pre-heating.
Cleaning Chemicals
Chemicals used in CIP systems include detergent, acid, extremely hot water, and chemical sanitizers. The product and standard operating procedures determine which solution is best for the cleaning process, all non-foaming. Sometimes the chemicals and water can be reused to save money; other times, a single-use system is best practice.
Automation
Fully automated or manual CIP systems are both options. Our in-house automation team works with customers to develop the PLC, operator’s interface, data communication interfaces, and data recording. Automated CIP systems provide consistency in the cleaning process and are worth the investment.
Additional Items
Besides the CIP system itself, there are a few other items to consider. Based on where the CIP system is placed in the plant, will there need to be washdown or explosion proof motors? Are there any space limitations? Are the correct utilities already on-site or will they need to be installed? Thinking through the complete process ensures the final design is optimized for efficiency.
For an in-depth look at specifying CIP systems or to chat about your CIP requirements, please contact us for additional information.
Learn more about our customizable solutions for liquid process systems.
AD Process Equipment is a Gray company.
AD Process Equipment is your single source for system design and process equipment integration. Our experienced team works with customers to meet demands in bulk processing and material handling by providing practical design solutions that cater to their unique needs. Our personalized solutions in equipment and technology give customers a competitive edge in the ever-changing global marketplace.