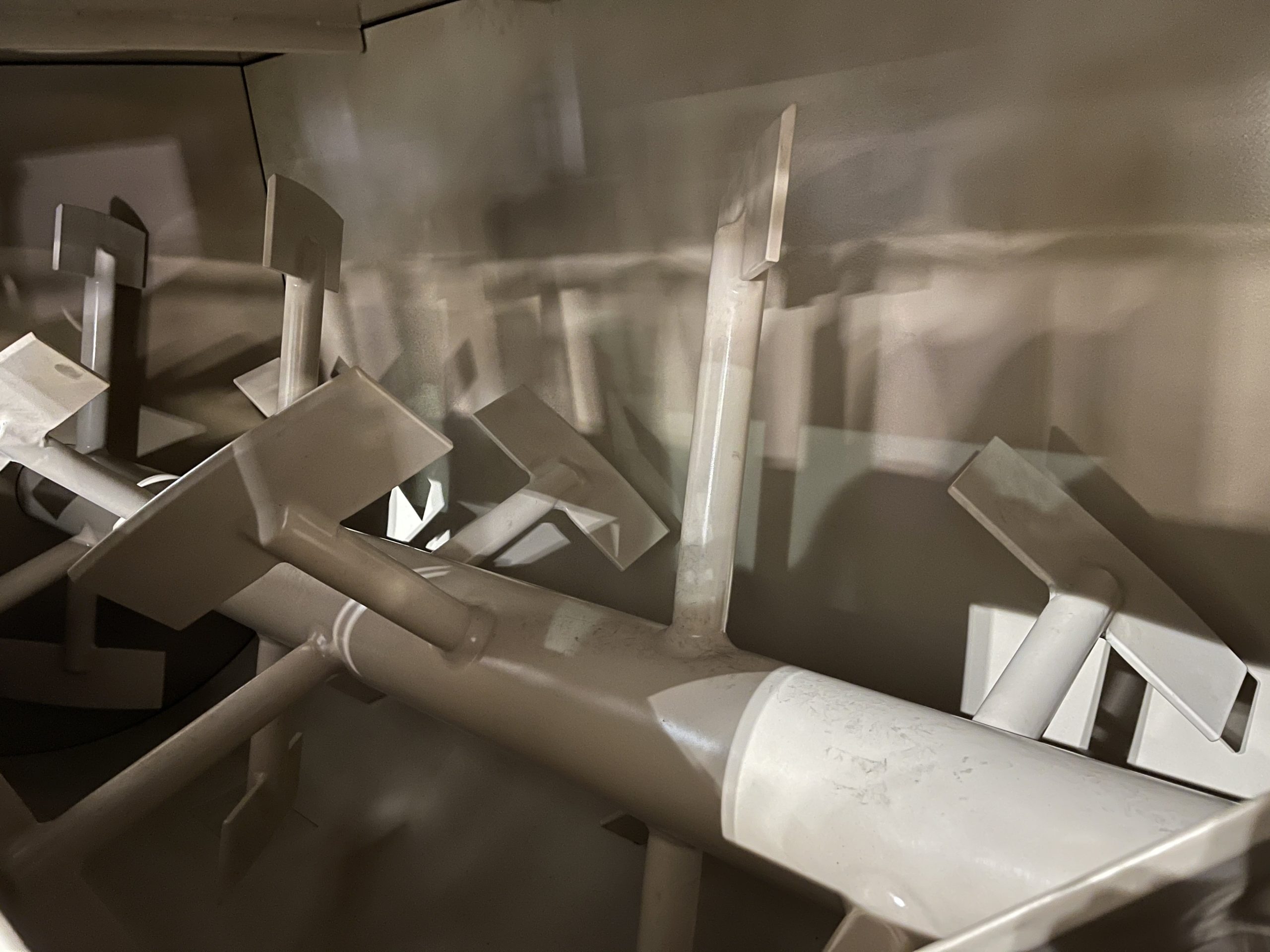
insights
Mixing Mechanics: Factors to Consider When Designing a Mixing and Blending Process
While many powder and liquid manufacturing operations use mixing and blending processes, each application has its own unique factors to consider. What doesn’t change from one application to the next are the questions you should ask when designing the process. These questions include:
- What type of material is it?
- What is its particle size?
- What are its flow characteristics?
- How will it settle after mixing?
The answers to these questions will help you determine each material’s ideal mixing system. After determining the best mixing, blending, and batching solutions for your material, you should consider the following topics as you go through the system design process. While each material and process are unique, the benefits of creating a perfect blend are universal.
Make Your Mix Accurate
When you make cookies, if the flour isn’t mixing in evenly or the baking powder is clumpy and not dispersing, you do your best to remove all the clumps as you hand mix the ingredients. However, one batch of cookies might taste slightly different from the next batch due to small mixing inaccuracies. You’re experiencing firsthand how mixing accuracy can be altered by just one ingredient.
For large commercial mixes, accuracy is even more important. Ingredients are expensive and brand consistency is paramount, so mixing accuracy is key to reducing ingredient waste and providing a consistent end product to your loyal customers. Your materials’ type, particle size, density, and flow characteristics will all play a role in ensuring an accurate mix each time.
Even a half-percentage difference in an ingredient could alter the end product drastically. While a half-percentage doesn’t sound like a lot, it could slightly change the product’s taste or color, impacting product consistency. Also, some products leave no room for error; for example, consider how important mixing accuracy is for a life-saving prescription drug product.
Accuracy becomes even more important when a blend contains ingredients with a variety of bulk densities. After the mixer has been running for a period of time, the ingredients may start to separate again. Knowing the blend’s proper residence time in the mixer will be crucial to successful mixing. Blends can also start to separate when they’re dumped from the mixer into a bulk bag station or pneumatically conveyed over a distance. You can alleviate these concerns by using smaller batch sizes, which yield more success when pneumatically conveyed, and by placing small mixers at the end stations, which can help to remix blends back to their desired end state.
Automation Leads to Quality Control
Automation can provide a level of consistency, efficiency, and quality control that hand batching just can’t match. Many food processes start out with recipes that call for one cup here and two cups there, all manually added. While hand batching a recipe this way is probably necessary when developing a product in the lab, the end product will only be repeatable a percentage of the time. Successfully transitioning from manual batching to an automated process is a critical step in product development.
If you go to your favorite fast food restaurant, you know exactly how your hamburger is going to taste, thanks to the company’s quality control process. The company only makes its ingredients in a certain number of locations using all the same ingredients, batches, and measurements. Automated processes ensure that your burger tastes the same whether you order it in California or in Florida. The same is true for bakery mixes, chemical blends, medications, and other commercial mixing processes.
A recent project for a chemical blending application reminded our team how important it is to accurately replicate the original mixture while providing efficient results. When dealing with hazardous chemicals, accurate mixing is critical. For the project, two blending systems were integrated into a 130-foot skid system. The blended mixtures for dry chemical powders were fed directly into bulk bags or rigid intermediate bulk containers. A hoist system was used to drop major and minor ingredients into two 100-cubic-foot horizontal paddle mixers, which were customized with a coating for the specific application.
The project increased the customer’s blending capacity up to 40 percent with batches of over 7,000 pounds. Implementing a minor-ingredient handling system improved the operator’s environment and reduced the manual process through controlled unloading of ingredients from flexible intermediate bulk containers (FIBCs).
Fully integrated equipment controls allow the system to be monitored remotely, increasing quality control, accuracy, and efficiency. If part of the system isn’t running efficiently, the controls immediately notify the customer and systems provider so they can address the issue.
Quality Control Includes Tracking and Sanitation
Besides providing consistent mixing accuracy, quality control should ensure that your products meet the appropriate standards for hygiene and sanitation. An automated mixing system can provide ingredient and lot tracking, which enables you to locate and dispose of all potentially compromised product if there’s a mishap on your production line.
To avoid those situations, facilities should have proper sanitation plans in place for not only the mixers but the whole process line. If your process is automated, a clean-in-place (CIP) system can minimize the potential for cross-contamination by providing automated cleaning cycles. CIP systems can be automated and scheduled to help operators stay on track and minimize downtime on the production line. Mixers with extractable shafts also help increase sanitation during cleaning.
Mixing Powders and Liquids
Some processes require you to mix dry ingredients with liquid ingredients, which presents additional challenges. Spray nozzles outfitted on the mixer must be thoughtfully placed to properly introduce the liquid to the powder in multiple locations inside the mixer. The number of spray nozzles, the spray pattern, and the material flow in the mixer all play a critical role in the success of the mixing process.
Lab-scale trials can be ideal for determining the best configuration while avoiding wasted material and resources. However, full-scale, installed equipment trials are still necessary to ensure that you have the proper configuration for your exact materials. Since each mix is unique based on material specifications, configurations will often be different depending on the situation.
You can mix dry ingredients with liquids using either batch or continuous mixers, but accuracy and repeatability are just as important as they are when mixing only dry ingredients. Testing will tell you which mixing configuration is best for your materials. Either way, the processes must be designed with sufficient residence, hold, and mixing time.
The pumps feeding the spray nozzles must be the appropriate type for the liquid’s viscosity and stickiness and must have sufficient flow and pressure ratings. Usually these are continuous-feed, nonpulsing pumps, and they are often on variable frequency drives (VFDs).
Spray nozzles are known to plug, so it’s a good idea to keep spares on hand to quickly swap out. Luckily, spare nozzles are relatively inexpensive, especially compared to the cost of having an inconsistent end product batch.
Some liquids will require that you flush the line with hot water periodically or between batches to keep the pump discharge and nozzle tips clean. Humidity levels can become a concern, so mixers processing hot fluids and batches often need a specially designed vent that allows moisture to escape but prevents condensation from re-entering the mixer. As with dry-only mixing, having a proper cleaning process in place is critical.
Originally published in the Powder & Bulk Engineering September 2021 issue
AD Process Equipment is a Gray company.
AD Process Equipment is your single source for system design and process equipment integration. Our experienced team works with customers to meet demands in bulk processing and material handling by providing practical design solutions that cater to their unique needs. Our personalized solutions in equipment and technology give customers a competitive edge in the ever-changing global marketplace.