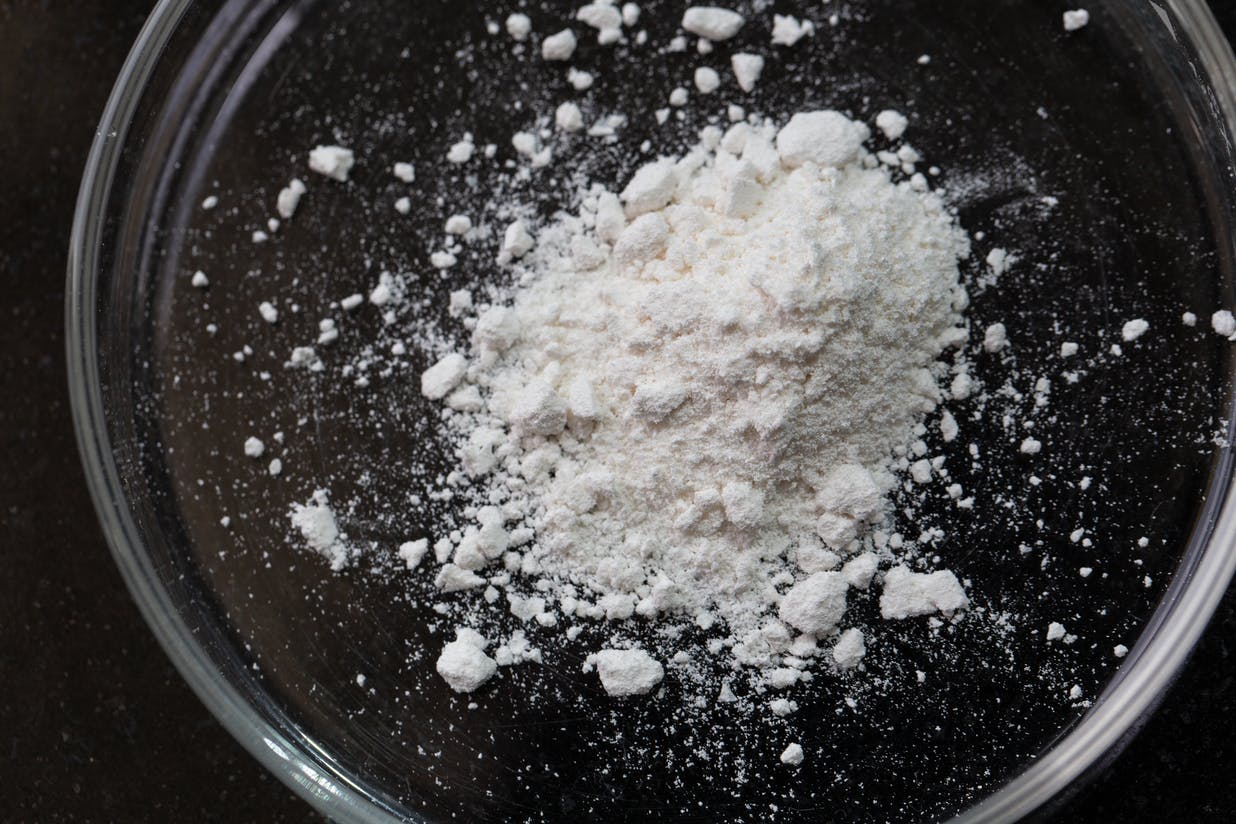
insights
Material Classification for Fine Powders
Originally Published in Processing Magazine
This article will explore the different types of classification technologies, including mechanical screeners – gyratory, centrifugal, vibratory, high-energy and ultrasonic – as well as air classifiers – both with and without classifying wheels.
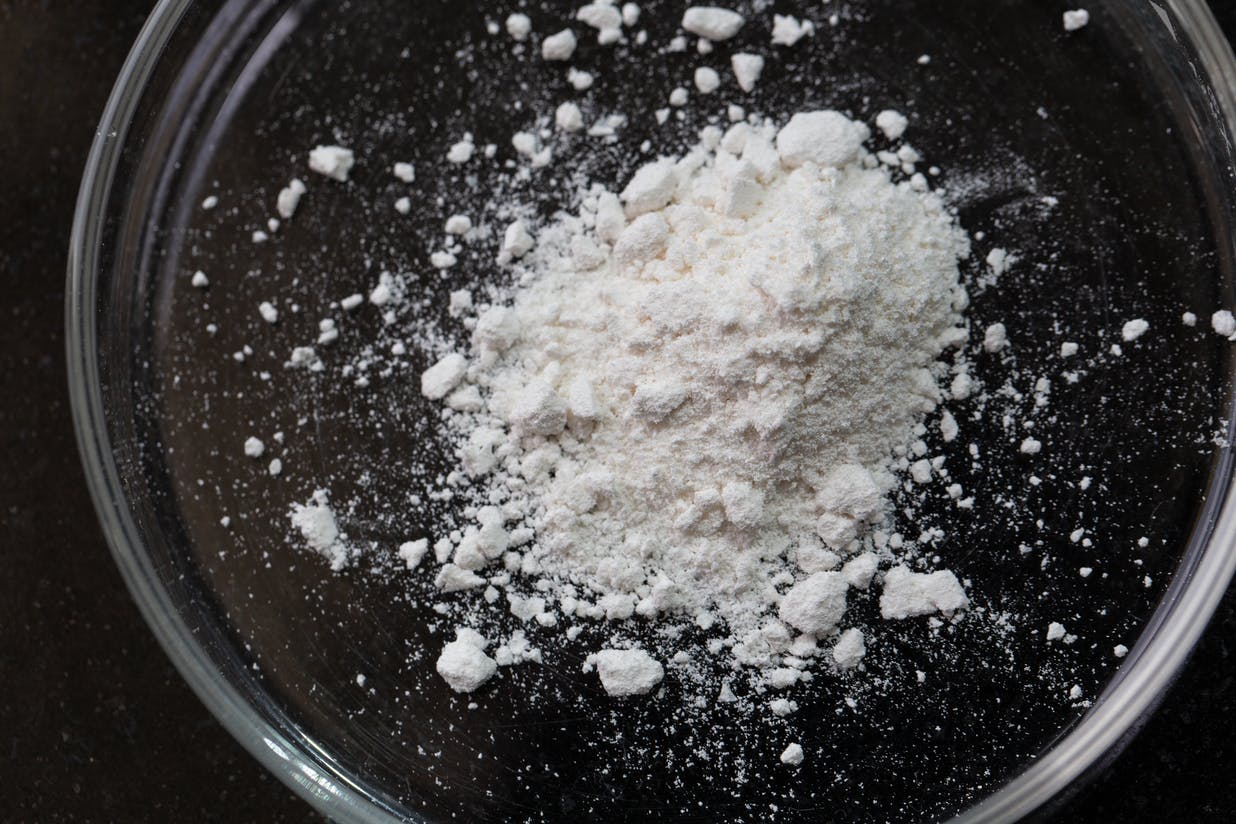
Fine powders often need to be separated by particle size to ensure uniformity and effectiveness in a mixture or product. However, because many material classification technologies are available, determining which type is most suitable for your powder can be challenging. It is important to take an unbiased look at the various powder classification methods available to identify the solution that will best fit your powder separation needs.
Understanding Your Material
To select the most suitable classifying technology, you must first understand your material’s particle size, shape and bulk density. With respect to particle size, simply stating a mesh size for separation is insufficient and leaves too much opportunity for error. For instance, is the mesh market grade, U.S. grade, tensile bolt cloth (TBC), stainless steel or nylon? To prevent errors, measure particle size in microns. A micron equals one-thousandth of a millimeter — too small for the naked eye to see. For instance, bacteria might have a particle size around 0.5 micron, while sand would have a particle size in the tens or hundreds of microns. Mesh-to-micron conversion charts are available online, if needed.
Particle shape is also extremely important. For example, a grain of rice appears to have a different particle size depending on whether it is being viewed from the side or from the end. It can be difficult to properly separate particles by size without knowing their true shape. Also, some particles have rough rather than flat or smooth edges. Such particles will have more difficulty passing through a square screen opening. Processing rates will vary depending on whether the particles are irregularly shaped or spherical.
A powder’s bulk density is its weight per unit of volume. For example, one pound of metal powder would fit into a small jar, but one pound of packing peanuts is going to be a huge bag. Depending on the material’s bulk density, the overall weight may be the same, but the volume of material being processed may be drastically different. This can quickly change the processing time for a classification process from a few hours to a few days.
Under the right conditions, most powders and bulk solids can be explosive. A thorough understanding of a material’s properties will reveal at what stages the material may present an explosion risk. For example, the granulated sugar in your kitchen cabinet is not at risk of exploding, but fine sugar dust is extremely explosive. Knowing the material’s explosion properties, including its KSt and Pmax values will help determine its tendency to ignite. KSt is a relative measure of a material’s explosion severity compared to other materials, and Pmax is the maximum pressure a material can generate during an explosion event.
It is also important to consider a material’s hygroscopicity, or ability to absorb moisture. Hygroscopic powders absorb water from humidity in the air, which increases their cohesion and decreases their flowability. For example, regardless of particle size, sugar will typically process at a completely different rate in the Midwest than it will in the Caribbean, because the Caribbean has a higher average humidity.
Finally, it is important to know the material’s particle size distribution (PSD). PSD is an index indicating what particle sizes are present in a material and in what proportions. For example, if a material has a D10 of 50 microns, a D50 of 100 microns and a D90 of 150 microns, then 10% of the particles are smaller than 50 microns, 50% of the particles are smaller than 100 microns and 90% of the particles are smaller than 150 microns.
AD Process Equipment is a Gray company.
AD Process Equipment is your single source for system design and process equipment integration. Our experienced team works with customers to meet demands in bulk processing and material handling by providing practical design solutions that cater to their unique needs. Our personalized solutions in equipment and technology give customers a competitive edge in the ever-changing global marketplace.