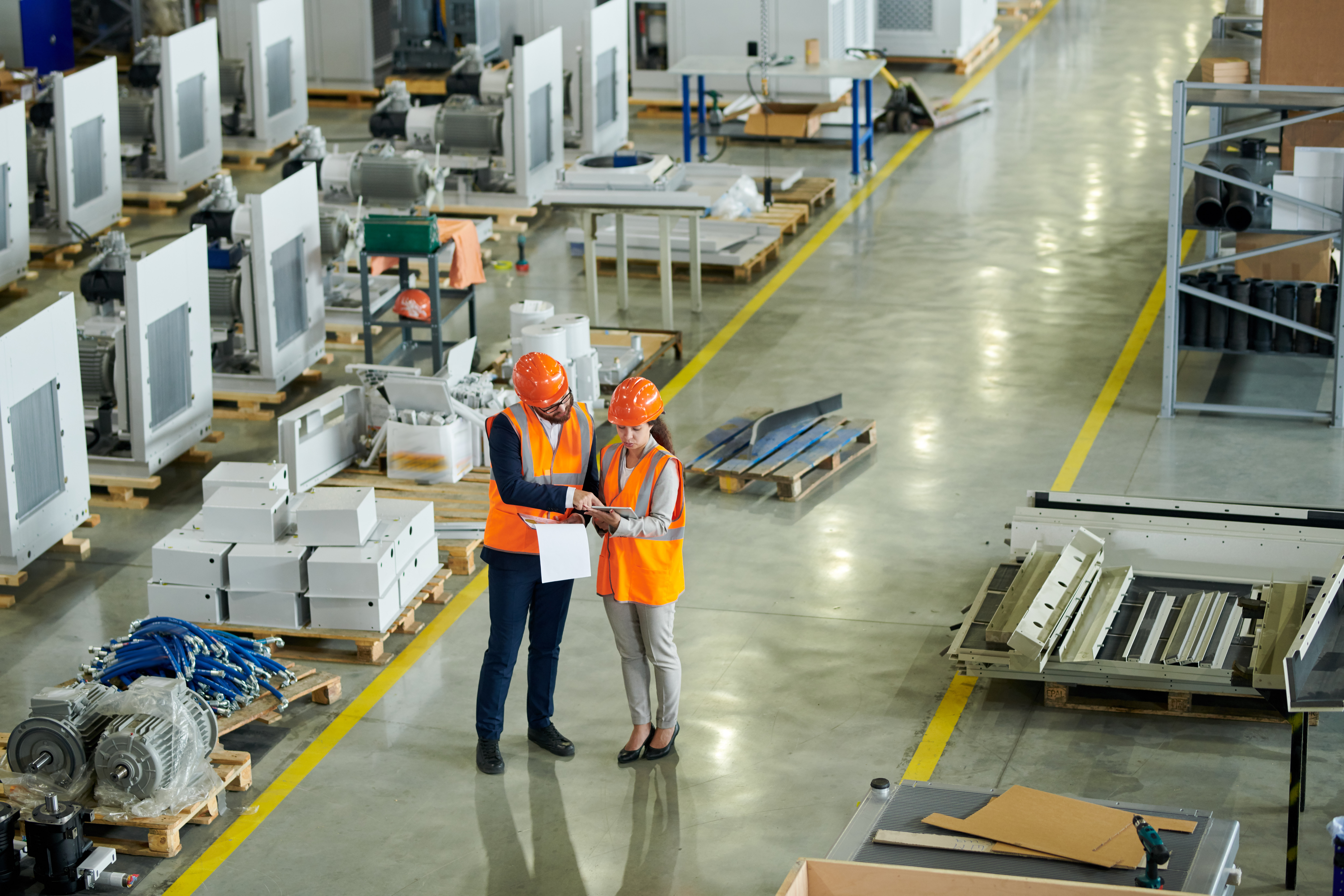
insights
Importance of Behavior-Based Safety Programs
Behavior-based safety programs are deeply rooted in Spec’s safety program, which includes the Gray Safety 7 and our ‘Safety in Action’ plan.
A behavior-based safety program is a process by which organizations raise awareness about safety issues by encouraging employees and management to evaluate their own behaviors and communicate with one another about safety issues. This is most effective when the safety team includes management as well as employees. At Spec, we value this line of communication and that is why we have a member of management on the Spec safety committee.
ARUP Laboratories reports that there are many factors that effect behavior, such as employee ability, corporate culture, and employee attitude. Typically, behavior is an observable act, and influence on one’s behavior is not different when it comes to behavior around safety.
It is important for companies to understand what motivates their employees, which includes both internal and external factors. These factors are what drives an employee’s actions and what they subconsciously think about when they perform their duties when on the clock.
Internal forces
|
external forces
|
Companies should also understand what motivates employees to take risks which includes saving time, convenience, comfort, laziness, workplace challenges, insufficient training, and unlikely negative consequences. While motivating factors can be fairly common throughout daily tasks, a good behavior-based safety program helps minimize these factors.
Part of Gray’s Safety 7 program is Decision Making which states that if you don’t know, stop and ask. Take a moment to consider the impact your decision can have on safety. Both of these concepts are rooted with the idea that behavior-based safety plays a key role in our safety program.
Sometimes unsafe behavior is rewarded, and do not always result in accidents or injuries. Eventually, this catches up with companies as near misses, injuries, exposures, and illnesses all start to build up. There are steps that can be taken by management to ensure that employees are thinking about their behaviors when in the workplace.
According to Safetymint, there is a seven-step process that can help in improving behavior-based safety in the organization.
- Identify critical problem behaviors.
- Identify root causes.
- Generate potential actions.
- Evaluate possible actions.
- Develop an action plan.
- Implement an action plan.
- Conduct follow up.
The outline of this program can be broken down into identifying unsafe behaviors, make a plan to fix those behaviors and communicating constantly to make sure these problem behaviors do not become habits. These ideas are reflected in Spec’s safety program with the Decision Making, Planning, and Communication stages.
Improved safety practices that stem from a behavioral shift from unsafe to safe practices is a large benefit of a properly implemented program and the key to any great safety program. Other benefits include increased awareness, situational preparedness, safer reactions, continuous feedback, and employee engagement.
Improved safety practices that stem from a behavioral shift from unsafe to safe practices is a large benefit of a properly implemented program and the key to any great safety program. Other benefits include increased awareness, situational preparedness, safer reactions, continuous feedback, and employee engagement.
Spec realizes the benefits of incorporating behavior-based safety points in our own safety program. Implementing sustainable and repeatable follow-up actions after the identification of unsafe behaviors is a worthwhile addition to any safety program.
AD Process Equipment is a Gray company.
AD Process Equipment is your single source for system design and process equipment integration. Our experienced team works with customers to meet demands in bulk processing and material handling by providing practical design solutions that cater to their unique needs. Our personalized solutions in equipment and technology give customers a competitive edge in the ever-changing global marketplace.